Ordering information: (Model) - (Thermocouple Type) - (Pre-Calibrated Temperature Range)
-
Select IRt/c(*) model. Example: IRt/c.3X
-
Select the thermocouple type (**) desired (J, K, etc.), add it to the model name. Example: IRt/c.3X-K
-
Select the target temperature range. For example, to control a lamination process at 200 F (93 C), look at the following target temperature table for 200 F (93 C). Note the black area in the table indicates the "180F/90C" pre-calibrated range. Add this to complete your selection. Example: IRt/c.3X - K - 180F/90C.
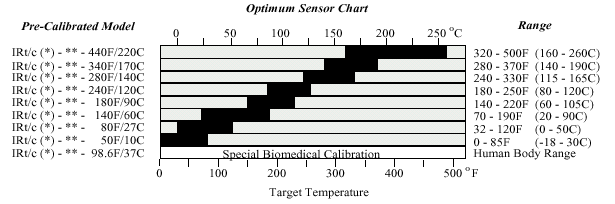
Additional note: The above table indicates the temperature ranges where the IRt/c's match standard thermocouple signals. This allows for highly accurate measurement and control in the ranges selected. IRt/c's require no power supply and can be connected directly to thermocouple inputs of controllers, PLC's, transmitters, and other t/c devices.
In addition, all IRt/c sensors are useable over the entire specified target temperature range for each sensor. Signal output tables and polynomials are available from Exergen.
Accuracy
IRt/c's are pre-calibrated at the factory for typical target material emissive properties, but actual emissivi-ties may differ. The accuracies specified assume that the precalibrated value is correct for your installation, or that the single point set up of Tech Note #1 has been performed to reduce the error to zero at the calibra-tion point (which is normally the set point for a temperature control system).
1. Using Non-Programmable Thermocouple Interface Devices
Standard non-programmable thermocouple input devices deliver a high level of accuracy and repeatability with IRt/c's for most temperature measurement and control of factory automation, process control and OEM machinery. For example, if an IRt/c is calibrated to measure and control a non-metal target at 200ºF (90ºC) set point, the error will be ±0% or ±0.02ºF (0.01ºC) at the set point. As the target temperature varies from the original set point temperature, the error increases slightly according to the Accuracy Table (below). For example, if the interface device is set for 0% error at 200ºF (90ºC), then at the extremes of the temperature range of 190ºF to 210ºF (87ºC to 99ºC), the error would be ±0.4% or 1ºF (0.6ºC). This gradual error is caused by a difference in linearity between the output of the IRt/c compared to standard thermo-couples. For detailed explanation, consult Tech Note #89.
2. Using Programmable Thermocouple Interface Devices, OEM, PLC, Computers
With programmable controllers, microprocessors, PLC, or computer interface, the error can be reduced to a small value even over a very wide temperature range. As shown in the Accuracy Table, IRt/c's produce high accuracies over a wide temperature range when the application requires it. For programming, contact Exergen for output signal tables.
Accuracy Table
|
*Percent is of reading. For wide target temperature variations, target emissivity variations may cause greater errors. Multipoint calibration is recommended in such cases, and can reduce errors to less than 0.1%.
3. Repeatability Error is < 0.01ºC (0.02ºF)
Repeatability error, defined as the ability of the IRt/c to reproduce a reading under the identical conditions, is extraordinarily small. There are no active electronics to shift, and no source of spurious signals until the limit of resolution is reached, which is 0.0001ºC, due to Johnson noise.
4. Interchangeability Error is ± 1% or 0.5ºC (1ºF)
Interchangeability error, defined as the difference in reading between any two IRt/c's of the same model making identical measurements, is of particular importance to users of multiple IRt/c's such as OEM's, or when an IRt/c must be replaced. The unit-to-unit consistency of IRt/c's permits the same calibration settings to be used for all subsequent installations for the same target material and temperatures. Inter-changeability specification applies only to the signal generated by the IRt/c in its precalibrated range.
Back to IRt/c Specifications
|